Use of the electrochemical potential to characterize the surface damage behavior of cyclically loaded materials
As part of the research project, a corrosion measuring set-up is to be set up and integrated into a fatigue testing system (rotating bending machine and/or vibration testing system) so that electrochemical investigations can be carried out. By exposing the materials to various corrosive and non-corrosive media (e.g. distilled water, acids, etc.), the medium-material interface reaction can be recorded in the form of the corrosion potential and current.
In further investigations, impedance measurements will also be carried out as an additional source of information for the investigation of the processes at the interface. In the project phase applied for, the aspect of non-corrosive media on austenitic materials (X5CrNi1810) is to be considered first.
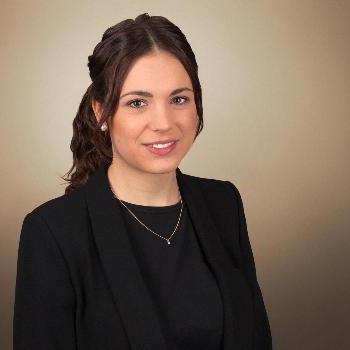
Wissenschaftliche Mitarbeiterin
- +49 631 3724-2015janina.koziol(at)hs-kl(dot)de
- Campus Kaiserslautern
- Room H1-2.010.2
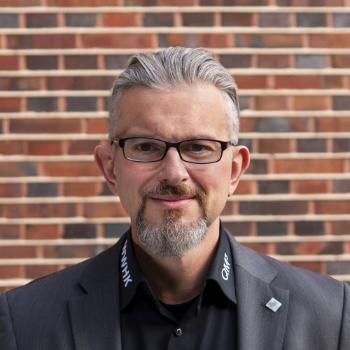
Vizepräsident für Forschung und Transfer, Studiengangsleitung: "Maschinenbau, Bachelor" "Mechatronik, Bachelor", Fachbereichsrat AING
- +49 631 3724-2389peter.starke(at)hs-kl(dot)de
- Campus Kaiserslautern
- Room H1-2010.1
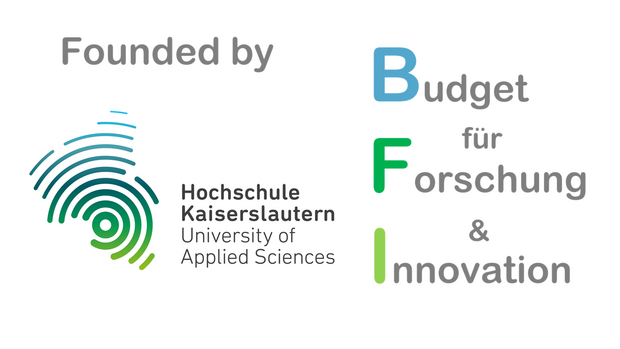
For the first experiments in distilled water, a miniaturized electrochemical in-situ cell with a standard three-electrode system, which is also used in potentiodynamic polarization measurements, is being developed. The challenge here is that the cell must be sealed at the sample shafts so that cyclic loading of the specimen can occur in the cell without the medium flowing out. The aim is that the change in electrochemical potential, after initial stabilization, can be measured under loading. Distilled water has no corrosive influence - especially for short test times - and therefore no influence on the fatigue behavior of the X5CrNi1810. The use of electrochemical measurement methods is very well suited here to detect microstructural changes on the surface. In the three-electrode system, a silver-silver chloride electrode (Ag/AgCl) is used as the reference electrode, a graphite electrode as the counter electrode and the X5CrNi1810 specimen as the working electrode. In these experiments, the gauge length of the specimen is in the corrosion cell. If, due to the cyclic loading, intrusion and extrusion effects occur, followed by microcrack formation on the surface, the oxide layers described above crack and the corrosion current increases and the corrosion potential decreases. If the cracking stabilizes, then re-passivation occurs, causing the corrosion current to drop and the corrosion potential to rise again to a stable value. Since surface damage is a continuously progressive process over the fatigue life, the degradation of the surface can be monitored and reliably characterized with the electrochemical potential. By comparing the current-potential and impedance measurements with additive measurement techniques based on electrical resistance, temperature or magnetics, different damage mechanisms can be separated from each other, resulting in a significant gain in knowledge from a scientific and application perspective.