Development of a short-term procedure for the evaluation of damage-relevant parameters of ferritic materials and components used in nuclear technology “EKusaP”
The overall objective of the research project is to develop a way to simplify the provision of fatigue data that can be used for both stress and strain-controlled loading situations. In addition, it should become possible to individually consider near-surface residual stresses as well as roughness values in the database. Since the determination of residual stresses by means of X-ray diffraction and the analysis of surface roughness can usually only be realized by destructive preparation of the components, indirect methods are to be used here. A µmagnetic measuring system is used for implementation in this project.
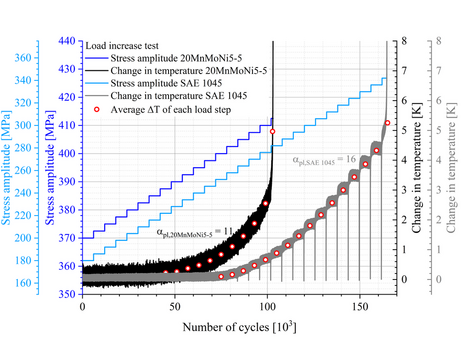
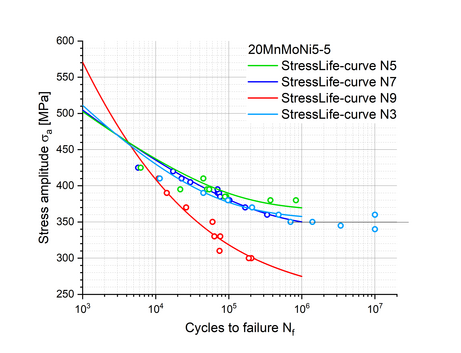
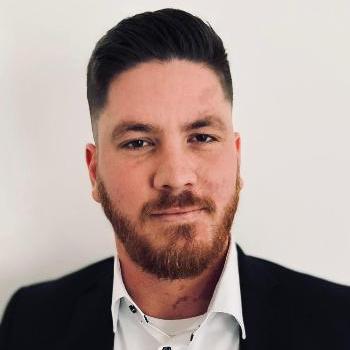
Stellvertretende Fachgebietsleitung
- +49 631 3724-2259fabian.weber(at)hs-kl(dot)de
- Campus Kaiserslautern
- Room H1-2.010.3
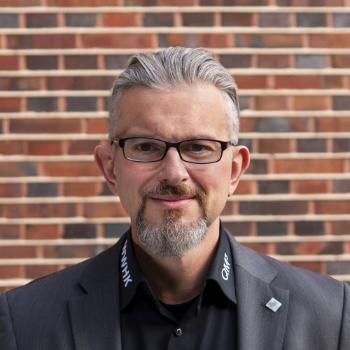
Vizepräsident für Forschung und Transfer, Studiengangsleitung: "Maschinenbau, Bachelor" "Mechatronik, Bachelor", Fachbereichsrat AING
- +49 631 3724-2389peter.starke(at)hs-kl(dot)de
- Campus Kaiserslautern
- Room H1-2010.1
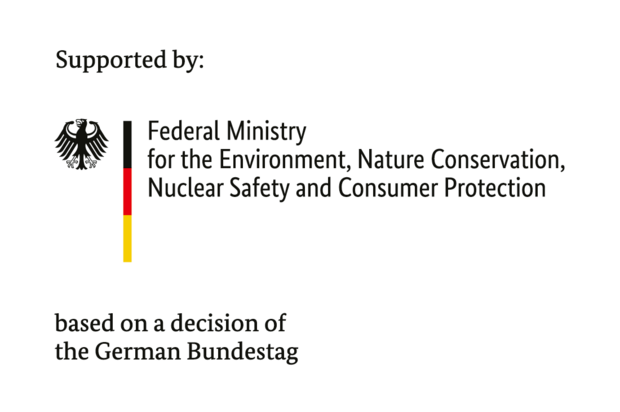
For this purpose, measurements on fatigue specimens are carried out on the steel 20MnMoNi5-5 in a service relevant heat treatment condition, in which the residual stresses are determined conventionally using an X-ray diffractometer and then the results are used in order to calibrate the µmagnetic measuring system.The surface roughness is measured using a confocal microscope and a tactile touch probe system. The fatigue data are determined in a stress-controlled manner and used for the generation of Wöhler curves using the StressLife fatigue life calculation method. StressLife offers the advantage that the fatigue life calculation is based on the material response and thus provides a basis for comparing stress- and strain-controlled tests.
The feasibility of these objectives is to be demonstrated in an exemplary manner within the framework of the research project and, if successful, can have a significant further widespread effect in application.
In the first step, the steel 20MnMoNi5-5 is procured, heat treated and then subjected to a comprehensive material characterization. At the same time, cutting inserts are modified for machining by grinding, cutting and polishing in order to achieve different surface conditions during the machining process. Five surface variants will be developed, which will be characterized by confocal microscopy, perthometer and X-ray diffraction. Subsequently, stress-controlled experiments will be carried out, first at room temperature and later at elevated temperatures (240°C and 340°C). The fatigue behaviour is characterised by means of strain, temperature (RT only), electrical resistance and µmagnetic measurement techniques (RT only or in load-free intervals) in load increase and constant amplitude tests. The fatigue tests are carried out according to the StressLife method, which is to be fundamentally developed further in this research project, taking into account parameters describing the specimens’ surface, and verified for application at elevated temperatures.
This approach opens up completely new testing and evaluation potentials, which can provide a comprehensive database for the residual life assessment of nuclear facilities.