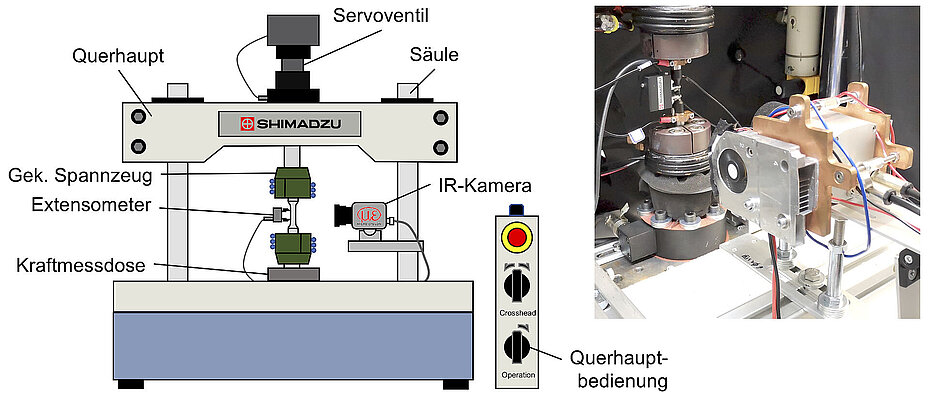
Experimental setup and material
The stress-controlled single-stage tests were carried out on a Shimadzu type EHF-U servo-hydraulic test system with a maximum load of 50 kN, a frequency of f = 5 Hz, a sinusoidal load-time function, and a load ratio of R = -1 at room temperature with RT = 25°C.
The specimens were stressed to failure or to reach the limiting load cycle number of 2×106 during the fatigue tests. In order to describe the alternating deformation behavior, the temperature change was continuously recorded during the test at the specimen surface along the measuring section(s) by an infrared camera of the type thermoIMAGER TIM 450 from Micro-Epsilon. This system uses the spectral range of 7.5 - 13 µm and has an optical resolution of 382 × 288 pixels and a thermal sensitivity of 40 mK.
The experimental setup is shown in Fig. 1 and described in detail in [4,5]. For thermal stabilization of the mechanical grips, a cooling system based on a Peltier element cooled water circuit was developed, which limits the temperature difference between the upper and lower grips to < 1 K during the test.
A normalized unalloyed steel of grade C45E was used as the test material. The specimens were machined from round material with a length of 5,000 mm and a diameter of 20 mm and subsequently polished to a roughness value of Rz < 6 µm. The chemical composition according to the manufacturer's specifications corresponds to the specified limit values according to DIN EN 10083 and is summarized in Tab. 1.
During heat treatment, the unalloyed C45E was austenitized at T = 850°C and then cooled to RT in a controlled manner, resulting in a predominantly ferritic-pearlitic microstructure with a Vickers hardness of HV10 = 216 [4,5]. In the tensile test, the material reached a maximum strength of Rm = 710 MPa and exhibited a yield strength of Rp0.2 = 413 MPa, resulting in a yield strength ratio of Rp0.2/Rm = 0.58. From these data, a predominantly ductile material behavior can be deduced for the unalloyed steel investigated.